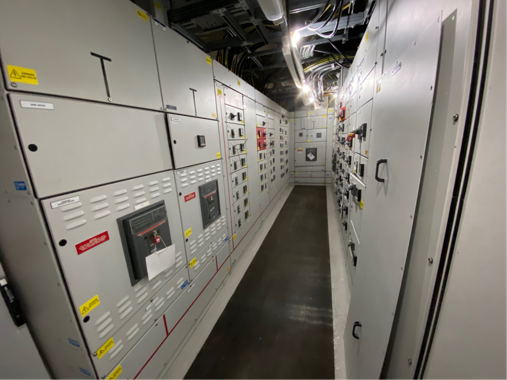
Introduction
In November 2021, Artic took over a university building that was experiencing regular power failures, blackouts and brownouts, which were disrupting research. Artic’s first task was to identify the cause of the outages.
Working with the university estates team and a nominated design consultant, we investigated several questionable elements installed in the HV and LV systems. We discovered that the existing Adamtech PLC system was obsolete and no longer supported by any software.
Actions
The existing PLC system crashed halfway through an unsuccessful scenario test. All parties agreed to replace it, beginning the procurement process for the best system for the facility. This involved numerous meetings with suppliers and stakeholders to ensure the selection of the most suitable equipment.
Challenges
One of the biggest challenges for this project was maintaining power supplies to laboratory equipment. It was important to keep this equipment running smoothly to avoid disrupting ongoing research, which could not be relocated due to the facility housing 25 years of research with an estimated insurance value of £30 million. The solution was to set up temporary generation as an N+1 configuration, providing all critical power via temporary distribution boards and commando leads ranging from 230V single phase (SP) to 400V three phase (TP). This ensured that essential equipment, such as laboratory grade fridges, walk-in freezers, freezer farms, comms server rooms, specialist ventilation systems, and reverse osmosis water systems (RO), would continue to operate throughout the project.
Solution
- Establish a project timeline and window for completion.
- Carry out any remedial work to the system that will not be affected by the upgrade, such as installing new generator components.
- Meet with end users to identify critical equipment that requires continuous power throughout the project.
- Survey the LV system of the building to identify all loads powered by the system, including the IOH and CHP.
- Survey the LV system of the building to identify all life safety systems that require continuous power, such as fire safety systems.
Health and safety
Health and safety must be considered for all works, including risk assessments, method statements, and permits. For this project, additional aspects had to be considered due to the building being regularly visited by lab technicians, such as:
- A site signing-in process
- Additional security and access control measures
- A health and safety board
- Life safety systems (such as fire safety systems)
- Temporary lighting and communications systems
Another issue was the fumes from the temporary generators, which had to be diverted away from neighbouring buildings.
Project overview – PHASE 1
Phase 1 involved installing temporary power supplies using generators. During this phase, we managed our client’s incumbents, which included access control, security, fire detection, lift systems, specialist lighting contractors, medical gas, communications, specialists, and lab equipment specialists.
- Access control was isolated and reinstated once the temporary power supply was live.
- Security isolated existing systems and provided additional staff to maintain security coverage for the duration of the project.
- Fire detection was isolated until the temporary power supply was provided and then reinstated once live.
- Lift systems were isolated and reinstated once the temporary power supply was live.
- Specialist lighting systems were completely checked and recommissioned where applicable once live.
- Medical gas specialists isolated the medical gas and reinstated it once the temporary power supply was live.
- Lab equipment specialist contractors isolated and reinstated the lab equipment once the temporary power supply was live.
Project overview – PHASE 2
Phase 2 involved isolating and stripping out the private HV (11kV) and LV (400V) networks. This included isolating two LV incoming supplies from two separate HV transformers and stripping out the existing LV mains infrastructure, including critical, essential, and non-essential switchgear panels.
The specialist subcontract services of access control, security, fire detection, lift systems, specialist lighting contractors, medical gas specialists, and lab equipment specialists were isolated and reinstated once the new LV system became live.
Project overview – PHASE 3
Phase 3 involved installing the new control panels (CoMAP) and LV switchgear. The remaining existing supplies and circuits were re-terminated into the new control panels and LV switchgear, which were then labelled with new control and LV schedules.
Project overview – PHASE 4
Phase 4 involved scenario testing and commissioning, which included having the site’s distribution network operator (DNO), witness the new G99 synchronization from generation to mains. To complete the project, we issued operation and maintenance (O+M) manuals on practical completion, witnessing documents for the scenario testing and commissioning, and record drawings.
Achievements and Outcomes
The successful completion of this project on a short timescale is an achievement in itself. Our staff worked in shifts to meet the required deadline of three weeks.
The newly installed electrical infrastructure is now an automatic switching system that can respond to different scenario mains failures. In the event of a complete mains failure (both incomers), the system will call upon the static generator on site to power all critical systems.
Impact
This project has made the specialist facility more resilient to power failures, blackouts, brownouts, and power spikes. The new automatic switching system will reduce call-out times and allow research to continue uninterrupted.
Recommendations
Because the client has more than 70 similar facilities, it is recommended that the CoMAP control system be standardised and rolled out to all critical facilities. This would provide the same level of resilience and reduce power failure downtime, allowing specialists to continue their work without interruption or interference.
Project statistics – temporary
- Temporary generators and fuel tanks: 3 x 500kVA generators and 3 x 3,000L fuel tanks were installed to provide sufficient power with some redundancy.
- Temporary fuel used: Seven refill visits over a two-week period, totalling 19,893 Litres of fuel.
- Temporary cables: 3,000 meters of temporary three-core and five-core SWA cables were used throughout the two-week period.
- Temporary supplies: Two 48-way three-phase distribution boards were installed per floor, from the ground floor to the roof (5th floor). Of the 48 spare ways, an average of 37 were used per floor to supply fridges, freezers, AC units, and other key plant.
- Temporary extension leads: 1,000 temporary extension leads were used.
- Temporary supply to IOH: A 100A three-phase supply was installed to maintain the operation of the IOH.
- Temporary supply to CHP: A 63A three-phase supply was installed to maintain general lighting, power, security, and life safety systems of the CHP.
- Temporary lighting: 20 x 8-10 hour battery site lights were hired and rotated to provide 24-hour coverage.
Project statistics – MAIN Project
- Cable totals: 2,970 meters of armored cable, ranging from 2-core to 27-core.
- Cable cores terminated: 1,826 cable cores terminated.
- Working hours: Artic employees worked an average of 16 hours per day for the bulk of the two-week period, totalling 224 hours per worker.
- Mileage: Each worker walked an average of 8.7 miles per day.
- Climbing: Each worker climbed an average of 37 flights of stairs per day.
SNAGGING AND REINSTATEMENT
After the project was completed, some reinstatement work was required due to the heavy traffic of workers and the numerous cable penetrations made for temporary supplies. This included:
- Fire stopping
- Floor cleaning and buffing
- General cleaning
- Waste removal
- Installation of a canopy for the CoMAP panel on the fourth floor
- Painting of the plant room plinth
- Labelling of cables
Meet the team
Collectively, the team boasts a combined experience totalling 380 years.
Share This Story!
If you're looking to partner with Artic Building, then please complete the Working With Artic form here.
Do you have an upcoming project or tender? Then please complete the form below.